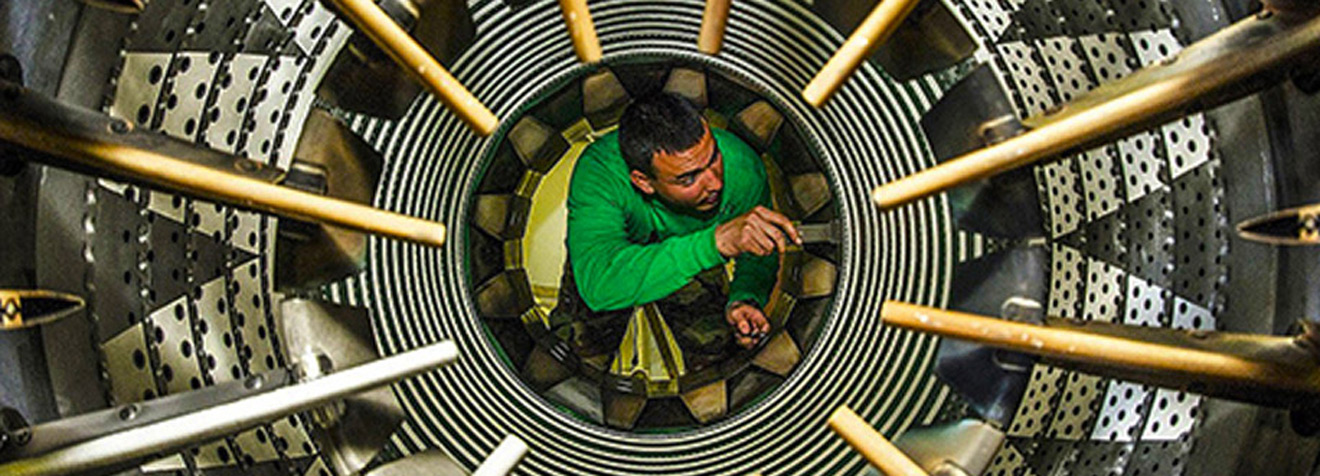
TPM Visión Global del Mantenimiento
| 15-10-2021Cuando empezó a consolidarse la producción industrial moderna, allá por los años 50, después de la Segunda Guerra Mundial, también empezó a imponerse una nueva preocupación por el mantenimiento de la maquinaria. Eran tiempos de crecimiento y (al menos el norteamericano) era un mercado musculoso y sano que demandaba orden y método para suplir las necesidades de un número de consumidores creciente y cada vez más exigente. Y la industria americana entendió que para maximizar beneficios, agilizar la producción, poder cubrir la demanda y, en definitiva, no perder el tren del consumo era básico tener los equipamientos industriales en perfectas condiciones. Todavía no había nacido el TPM, pero las bases ya se habían establecido.
Un trabajo de equipo para los equipos
La filosofía o metodología del TPM, sin embargo no es americana. Es japonesa. Y no tiene sus orígenes en la posguerra, sino en la recesión mundial de los años 70. Una de sus claves es la consecución de los Tres Ceros: Cero Averías, Cero Defectos y Cero Accidentes. De este modo, se consigue una eficiencia segura y progresiva en cualquier sistema productivo.
Precisamente por esta necesidad de maximizar el rendimiento de los equipos, la metodología TPM no entiende “equipo” sencillamente por “maquinaria”. Equipo también se refiere a equipo humano. Y en este sentido, eso supuso una gran novedad. No sólo por empezar a preocuparse de las personas, sino también porque al preocuparse por ellas aparecieron algunas preguntas: ¿cuál sería la mejor manera de aplicarlas?; ¿cómo se podría aprovechar su conocimiento directo de las mecánicas de producción para conseguir eficacia productiva?; ¿qué valor aportan a la industria más allá de la fuerza de trabajo? Todas estas preguntas cristalizaron en una inclusión del equipo humano en la TPM y en un aprovechamiento de su experiencia y conocimientos.
En cierto modo, la “mejora” que incluyó la industria americana en su metodología productiva ya se apoyaba en la experiencia directa y los conocimientos adquiridos por los operarios. Y la industria japonesa lo tuvo muy en cuenta para forjar el TPM. La división del trabajo en “productores” y “reparadores” desapareció, y ahora cualquier operario se ocupaba de todos los aspectos de su equipo. No sólo producía con él. Era responsable de él. Así, estaba más implicado en su trabajo y, sobre todo, la productividad empezó a ser mayor.
La importancia del mantenimiento
En futuros artículos, ya profundizaremos en los pilares, las metodologías concretas y otras características específicas del TPM. Hoy, en esta introducción a un tema que nos parece crucial para nuestra industria nacional, queremos terminar apuntando que uno de estos pilares (puede que el más importante) es la conservación, limpieza y optimización de los equipos con productos de mantenimiento específicos, que es algo en lo que tenemos mucha experiencia aquí en Kripton.
A día de hoy existen normativas que regulan el mantenimiento indicadores de mantenimiento que generan normas como.UNE-EN UNE. AEN/CTN 151- MANTEMIENTO.
Es el comité que se encarga de la normalización de las actividades de mantenimiento y han generado normas como UNE-EN UNE 151001:201 1 Mantenimiento. Indicadores de mantenibilidad de dispositivos industriales. Definición y evaluación o la UNE-EN 15331:2012 Criterios para el diseño, la gestión y el control de servicios de mantenimiento de edificios.
Mejoras enfocadas
El pilar de mejoras enfocadas exige que todas las ingenierías y departamento de carácter técnico sumen sus esfuerzos en la misma dirección: instalaciones y máquinas, procesos de producción, mantenimiento, compras (por el contacto con los proveedores como parte del equipo humano), determinadas secciones de logística y, sobre todo, la seguridad y el medio ambiente, coordinados para afrontar los problemas del día a día, formando grupos de trabajo de múltiples especialidades que compartan y contrasten puntos de vista y den soluciones y aplicar a otros puntos de la fábrica, aunque sólo sean una parte del problema y haya que seguir investigando en él.
Gestión temprana del mantenimiento
En el pilar de la gestión temprana del mantenimiento, se potencia la ingeniería de mantenimiento participando en el proceso de diseño de nuevos equipos. En la realización de los pliegos de condiciones para adquisición de nueva maquinaria, en las especificaciones de mantenimiento que plasman unas condiciones para que la maquinaria nueva venga adaptada a las necesidades de usuarios y mantenedores. La ingeniería de mantenimiento debe hacer constar los puntos débiles de la máquina, así hacer un seguimiento más cercano (incluyéndose en el preventivo y/o predictivo), así como realizar la lista de repuestos más críticos para adquirirlos y ubicarlos en Kankan en la línea.
Son las bases del lanzamiento del TPM en la fábrica. Sobre todo, debemos centrarnos en la parte humana de estas bases, pues es el punto fuerte y, paradójicamente, también débil de todo el esfuerzo. Dentro de las bases del fundamento de las etapas son: preparar, desarrollar, optimizar y dentro de estas etapas podemos encontrar las campañas de formación técnica, estructura y estrategia, en la actualidad existen 12 etapas propuestas por TPM.
Implantar la herramienta TPM exige (al piloto o responsable) poseer un espíritu flexible, una mentalidad vanguardista, un carácter robusto ante la desmoralización, y capacidad de transmitir todo ello a su equipo humano.